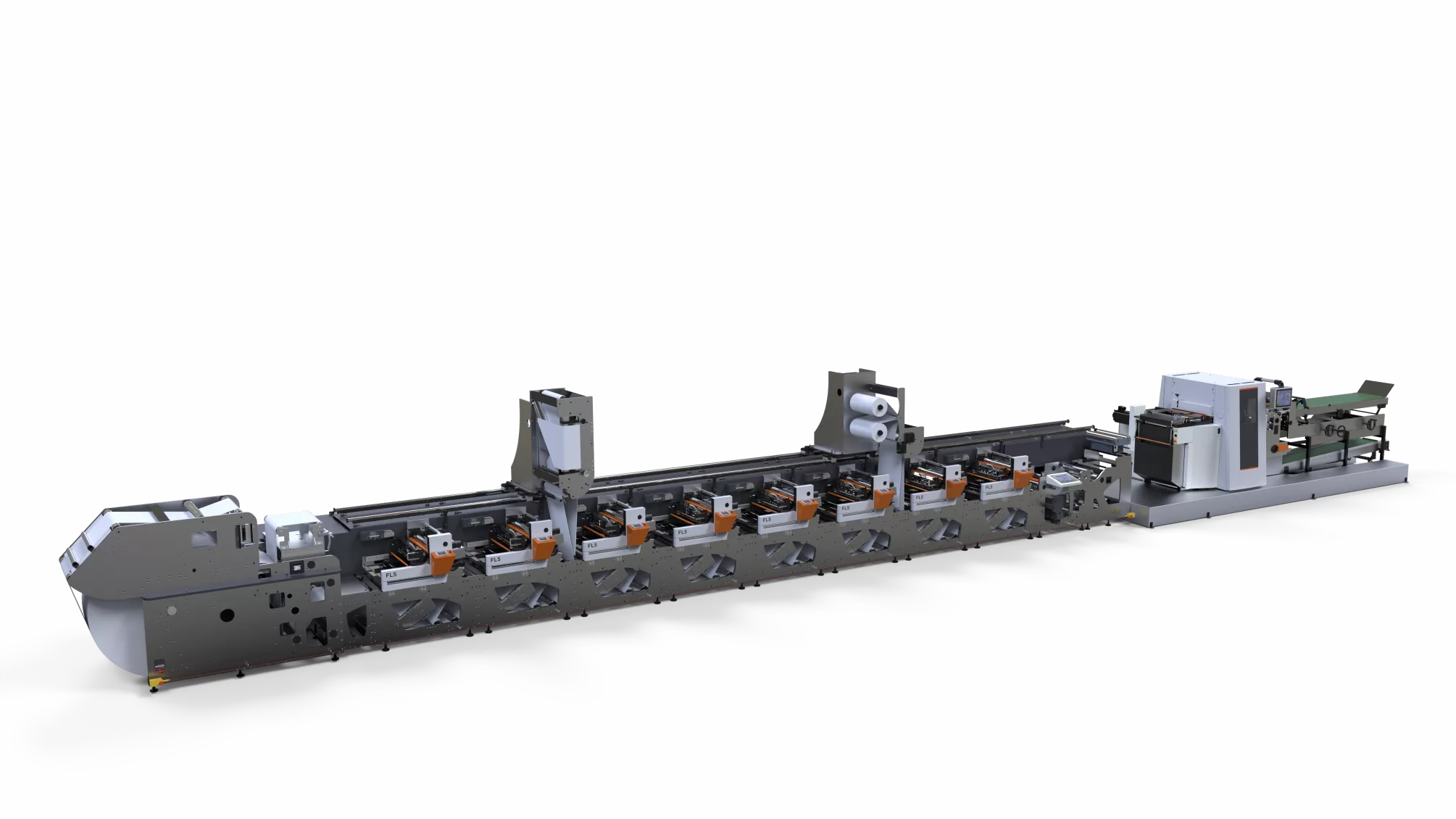
EXCLUSIVE INTERVIEW FOR FOLDING CARTON INDUSTRY, EDALE’S MANAGING DIRECTOR
JAMES BOUGHTON SPOKE WITH NICK COOMBES
THEY DISCUSSED THE PHILOSOPHY AND TECHNOLOGY BEHIND HIS COMPANY’S LATEST PRESS FOR THE CARTON MARKET AND WHY HE HAS HIGH HOPES FOR ITS SUCCESS IN THE INTERNATIONAL ARENA.
FCI “Before we look at your new generation press, can you give us the background to Edale’s involvement in the folding carton market?”
JB “The company has been engaged with supplying technology to the package printing industry for more than 75 years, but the carton aspect began back in the mid 1990s when we developed our 510mm wide inline flexo carton press that was first shown at IPEX, at that time with rotary die-cutting. However,
the major breakthrough came with the launch of our flatbed die-cutter in 2010, which we knew was an essential element for success with inline carton production. But, in reality, the company had been interested for some time in this diversification from the highly competitive label market. Where other narrow
web press manufacturers were looking at flexible packaging and shrink sleeves with filmic substrates as diversification, Edale saw the folding carton market as the best way of offering added value to converters.”
FCI That was quite bold decision wasn’t it, considering the existing market for carton production?
JB “Well, yes, and no! In Europe we knew we would have a tough job convincing the carton houses to switch from their long-held approach of sheet fed offset with offline converting, especially as the major press and converting technology manufacturers were based here. But in the USA, for example, inline flexo was already a well-accepted and proven process, and other international markets were, shall we say, a little less blinkered in their thought process towards production. So, we knew there was a demand for this type of press, all we had to do was come up with the right technology to make it work.
When did it begin for real? JB “We launched our first carton press in the 1990s, but it was not until the development of our Gamma line and flatbed die-cutter in 2010 that we started to establish a solid foothold in the carton market. We knew that adapting a label press would not work so we started from the ground up with a new design that principally involved a more heavyweight construction to be capable of handling the additional stresses that cartonboard makes over label stock. Everything from side frames to rollers and drive train as well as some less obvious print process related nuances needed to be capable of printing and processing any cartonboard that a sheet fed offset press could cope with if we were to convince traditional houses to consider our proposition. It was a massive investment but has paid great dividends, because now more than 50% of our overall business is in the carton market.”
FCI Traditionally, offset print quality is seen as superior to flexo – how did you overcome this?
JB “We didn’t have to in fact. If you go back a few decades, flexo was no match for offset, but if you look at the developments that have happened like CtP, UV inks and lacquers, better anilox rolls, and so on, there is very little now that flexo cannot do, and in most cases the colours are far more vibrant than offset, which if you’re looking for on-shelf impact in the supermarket, is a big bonus. I think the case for flexo being a quality print process is now well and truly proven and accepted globally.
FCI “What would you say is the major hurdle you have to overcome with the market?”
JB “Despite the obvious advantages of inline flexo, which I’ll go into later, there is still a reticence out there – a belief that it cannot possibly be as advantageous as it appears – sort of ‘too good to be true’.
I think It’s not so much having to overcome the fear of moving from offset to flexo or even sheet fed to web fed, it’s the fact that people cannot get their head around the improved workflow, the smaller footprint requirement, not only of the machine but the work in progress too, the single person operation for all processes, and the one-pass production from blank roll to finished product, including all types of embellishment. If you’ve only ever known traditional carton production methods, it’s a lot to take in all at once.”
FCI “Is that where you see your main market?
JB Absolutely not. What our new generation FL5 offers is effectively the same print and converting capability as a B2 format offset press and die-cutter. It’s likely that most, if not all, carton houses will have this capability in-house, but for much of the added-value embellishment that is now in high demand, they will be outsourcing work.
If you think of the different processes that are often required from printing through cold foiling, hot stamping, embossing and Braille, lacquering, and die-cutting, each of which requires work to be down-stacked for separate processing, then add up the floorspace and time that all this requires, the argument for single pass inline production is well and truly made. We see our prime market with existing carton houses that are looking for a more cost effective way of handling short to medium run high value work with a fast turnaround, because time to market is critical and is what every Brand Manager wants. Aside from the improved production efficiency, consider the reduction in costs: lower Capex, shorter ROI, reduced labour costs, less floorspace, lower power consumption, cheaper carton board on the roll, and so on, then it really is a ‘no brainer’.”
FCI “Let’s look at the new press in detail – can you take us down the line and point out the key factors that carton converters need to know?
JB In standard form it starts with a large diameter 1500mm (60″) unwind, which of course can be replaced with automated options for continuous operation if required, and the press is fully servo driven to allow it to handle a wide range of board thicknesses. It has preregister and print head automation, which combined with a short web path makes for minimal waste. Its print head geometry offers consistent repeats with minimal adjustment, which is especially useful for short runs, and it can handle a colour change in under 60 seconds without the need for tools.
The overhead rail offers almost infinite flexibility of converting and embellishing options, and job set up and storage is from a single HMI point. The inline flat-bed die-cutter provides cut, crease and emboss facilities combined with low tooling costs and automatic waste stripping, and it has a delivery system that de-nests the blanks for easy collection.”
FCI “I know you’re basing your rationale on seven key challenges that carton converters face – can you explain what this means?”
JB “They are all fairly obvious, but when added together and analysed, they highlight how inefficient the traditional carton production method really is. Let’s start with the excessive set up time and waste involved in using offline machines – single pass does this in one operation. Offline machines are expensive to buy
and run – our automated inline option is not. Offline needs more operators – ours needs just one skilled operator. Multiple machines require more floorspace – ours has a compact footprint. Offline needs space for WIP – we don’t. The increase in SKUs is difficult to handle cost-effectively offline – but easy inline. The offline production process is fragmented which means longer delivery times – we can be quick to market, in some cases same day. They are all simple but critical to production efficiency and cost-effectiveness – and in today’s highly competitive market, anything that gives you an edge over your competition is valuable.”
FCI “I guess seeing is believing – so how do interested parties find out more?”
JB “We are keen to welcome any carton converter who’d like to see a demonstration of the new FL5 single-pass carton production line to visit our showroom facility in Whiteley, Hampshire, and if they wish, they are welcome to run one of their existing jobs on the press for true comparison purposes – that’s how confident we are in its ability to match anything the traditional method can achieve. If they can’t make it in person, we’re more than happy to set up a live video link to show them what the press can do.
FCI How would you sum up the importance of the third generation FL5?”
JB “It brings inline flexo carton production bang up to date with the best technology and automation that you need to satisfy even the most discerning customer – and it does it efficiently and economically. It’s the perfect complement to existing carton production methods and offers both new and seasoned converters a real opportunity to make money.”
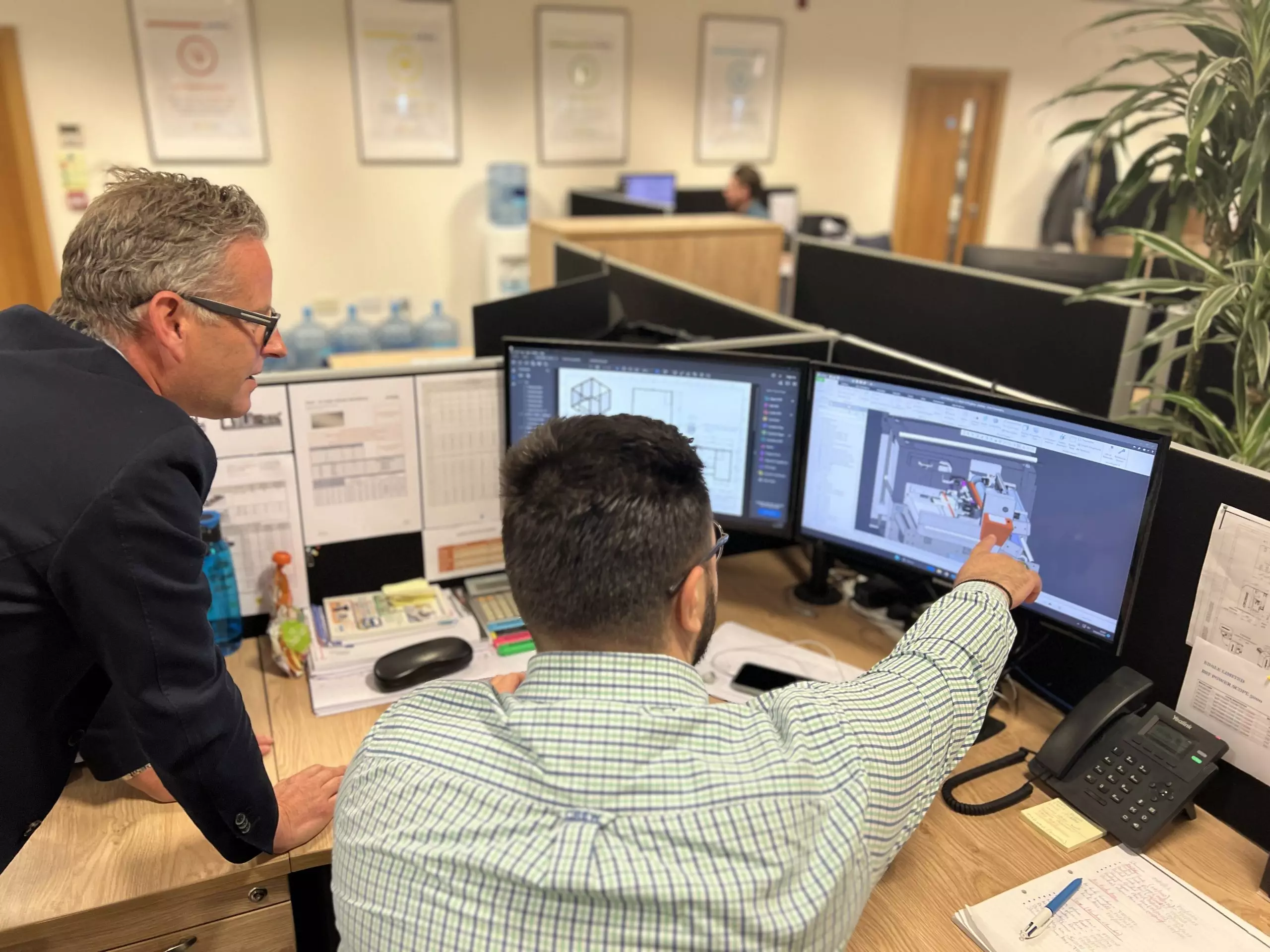
James Boughton inspecting a new drawing with a member of the Design Team.
Samples of flexo cartons run off the new Edale press.
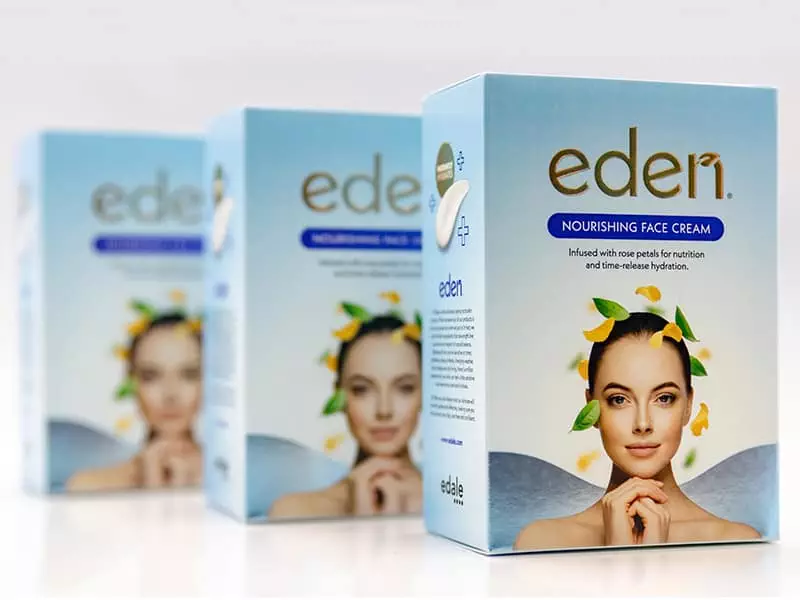
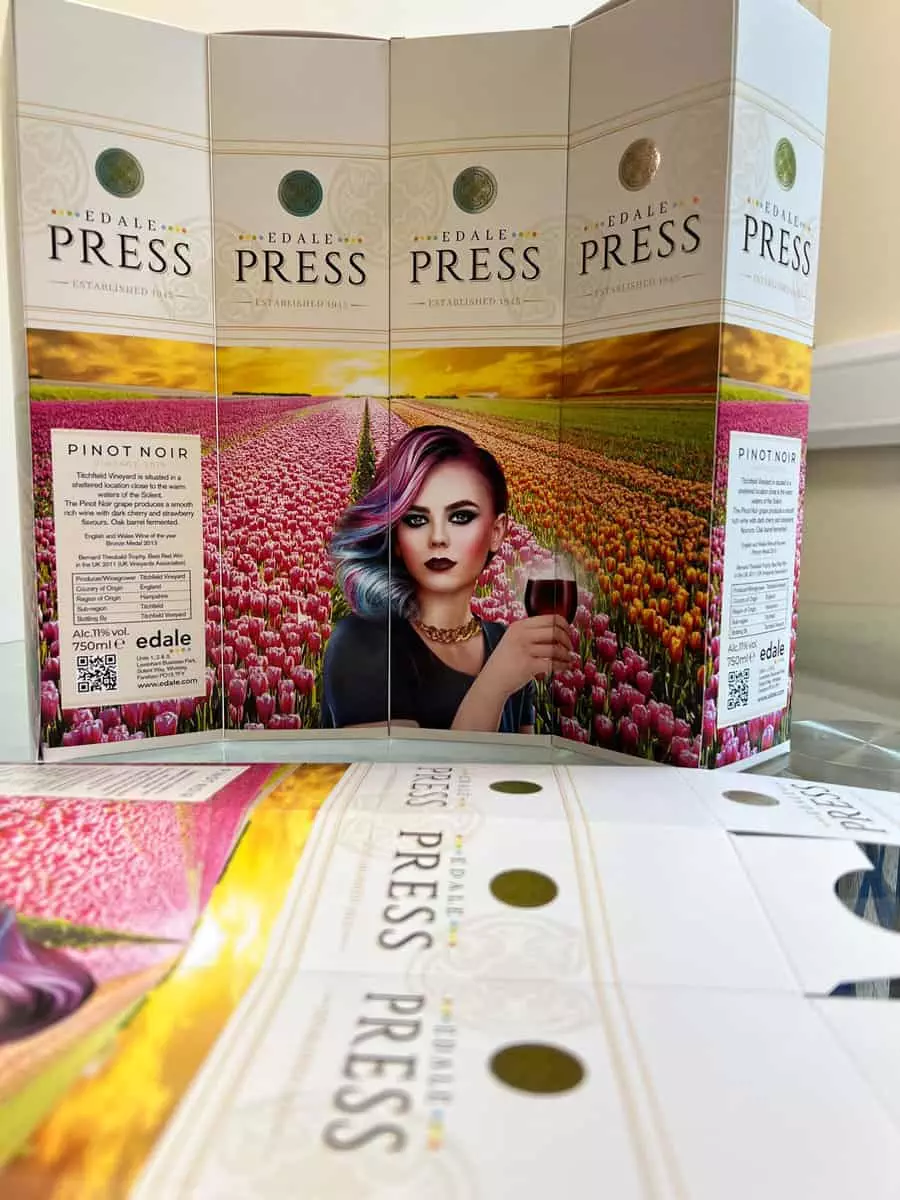
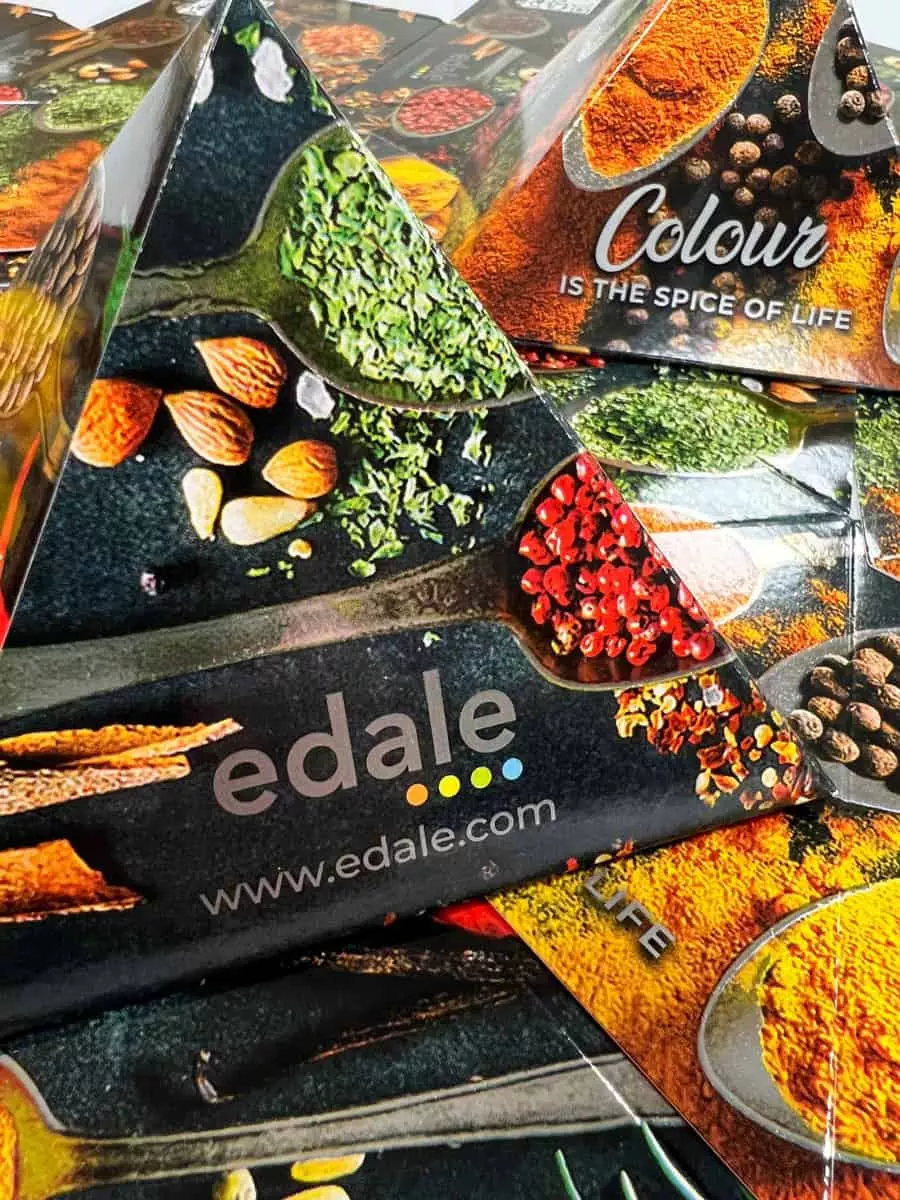
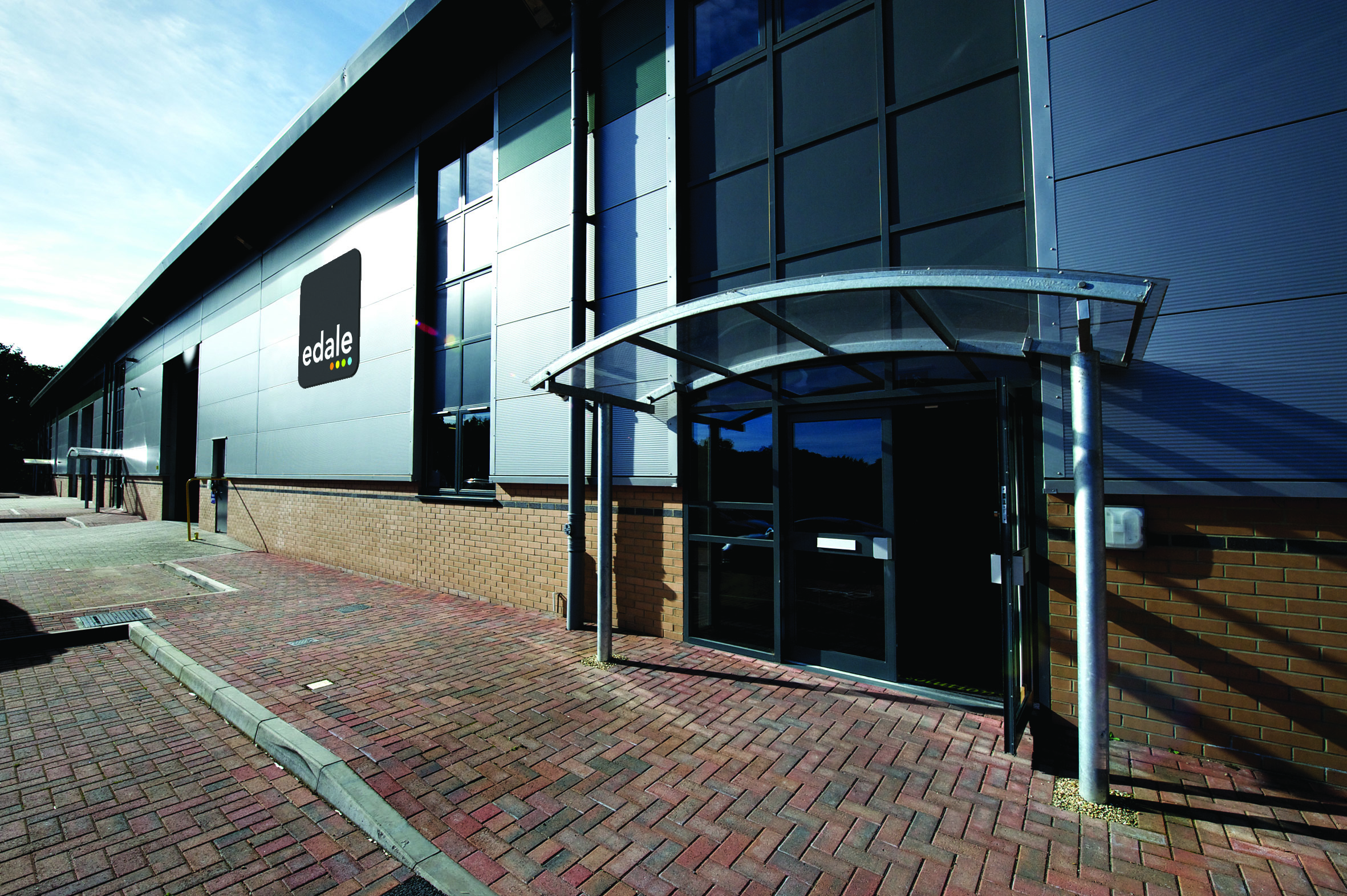
The new FL5 is available for a production demonstration at Edale’s modern facility in Whiteley, UK.